Episode 92 – 5 Misconceptions Shippers have about Setting up an EDI Connection with a Carrier
In this episode, we breakdown 5 ways shippers get tripped up when setting up an EDI connection with a carrier. To help explain the misconceptions and what you can do to course-correct them, I’ve asked Aborn’s Data Integration and Implementation Manager, Bill Muse to join the show.
1. EDI is the same for everyone
Often you'll find that EDI specifications are not the same for everyone and that's because while the technology is the same, the utilization is not. Just because you set up a connection with Estes does not mean the same parameters will work with SAIA. A great analogy is most people have hair on their head but it doesn't mean everyone has the same set of hair. EDI connections can and usually are unique to the carrier so a new connection will need to be made based on what the carrier is appropriating with the technology.
2. EDI will solve all communication problems
EDI is great at telling you when things go right with a shipment but not when something is off. You will still need to have a good relationship with your carriers, 3pl's, and freight forwarders to know why there was an error with the delivery. This is because very few carriers employ the capabilities to relay the status that something is wrong. If you have a good relationship, you will find they are more comfortable telling you when problems arise. Technology will not solve that issue.
3. EDI will do anything
While the technology has a massive subset of things it can do, the amount it is actually used in the freight world is very limited. We often find this is the case because of the amount of work it takes to set up and maintain the connection. Yes, it can do a lot of things well, but it cannot do anything.
4. EDI covers exceptions
Garbage in, garbage out. EDI tells you what is moving and what you said you put in there. EDI will not tell you if the shipment was delivered to the wrong place, if the wrong thing was loaded into the trailer, or if anything was damaged during the transit. EDI is there to cover the human error in data entry, not in the actual delivery of the freight or invoices.
5. EDI is set it and forget it
If you set up EDI and everything is working today it doesn't mean that something on the other side of the connection cannot change. In our ever-changing world software updates are commonplace and with updates comes the chance for something to change in the connection. We are constantly going through our connections during each update to ensure none of our processes broke. Even after you monitor software updates you are still susceptible to human errors so there is always the need to monitor connections.
Thank you for listening!
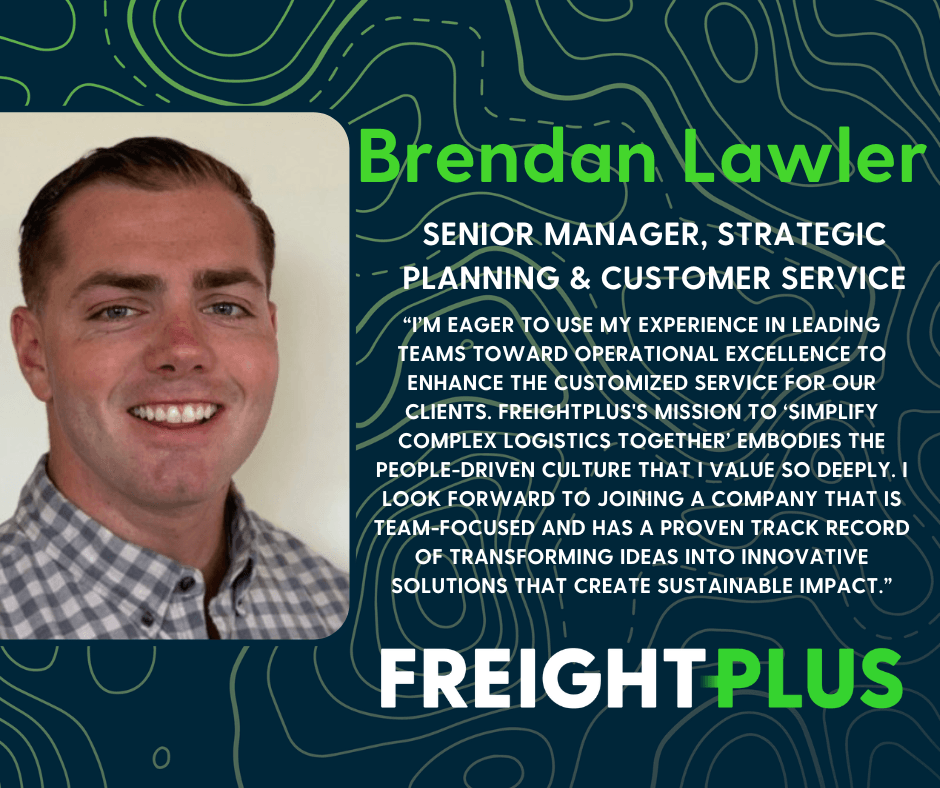
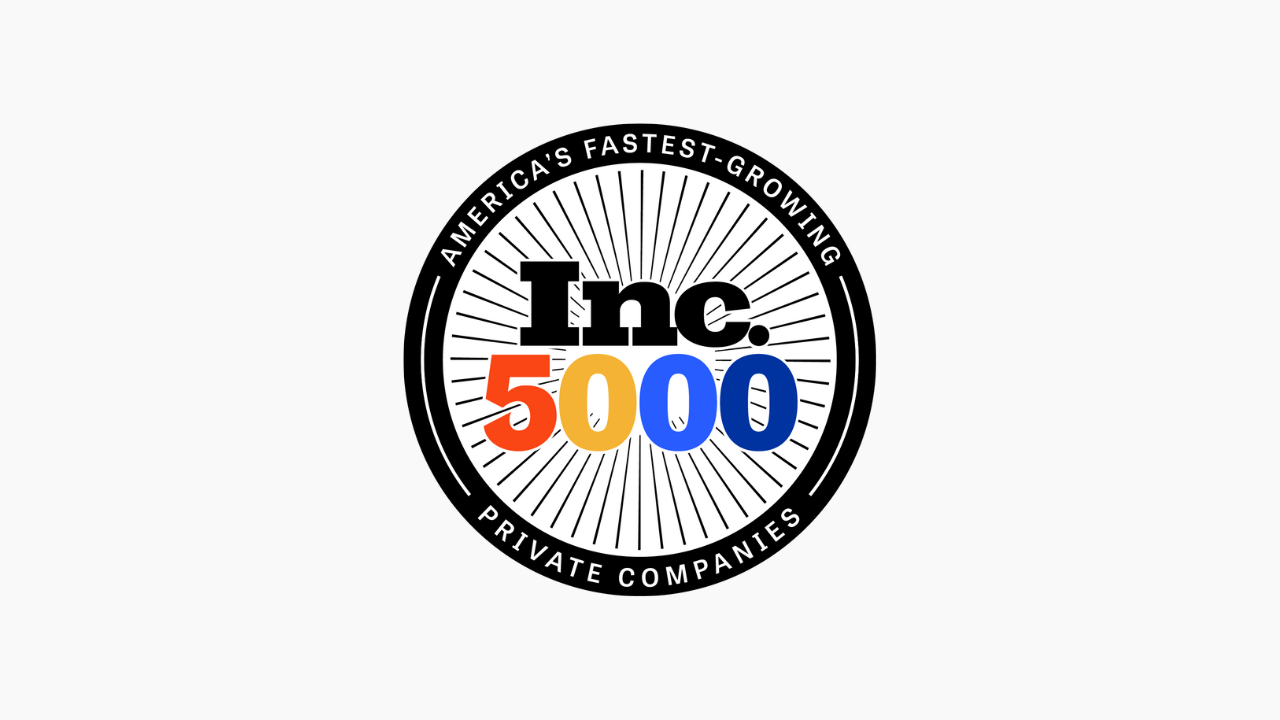
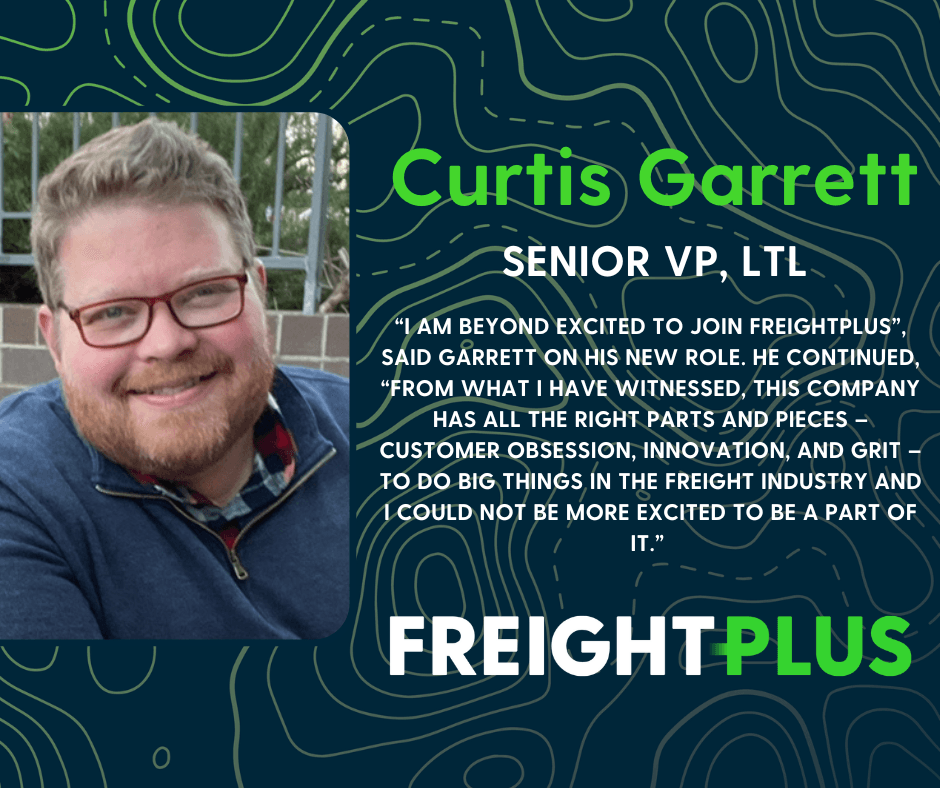
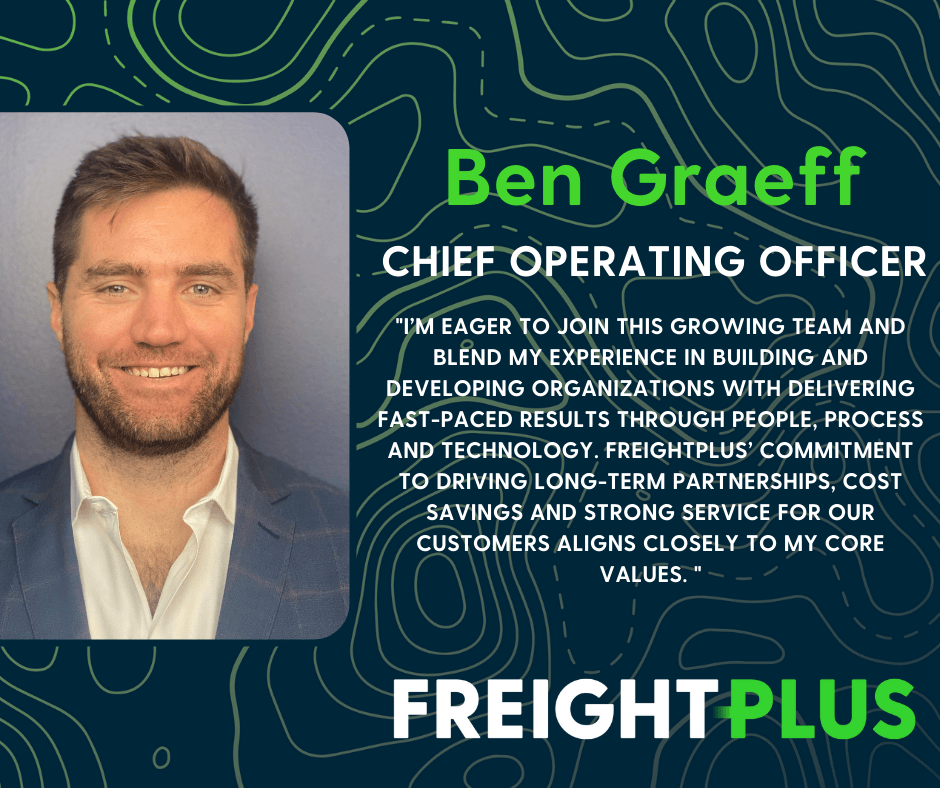